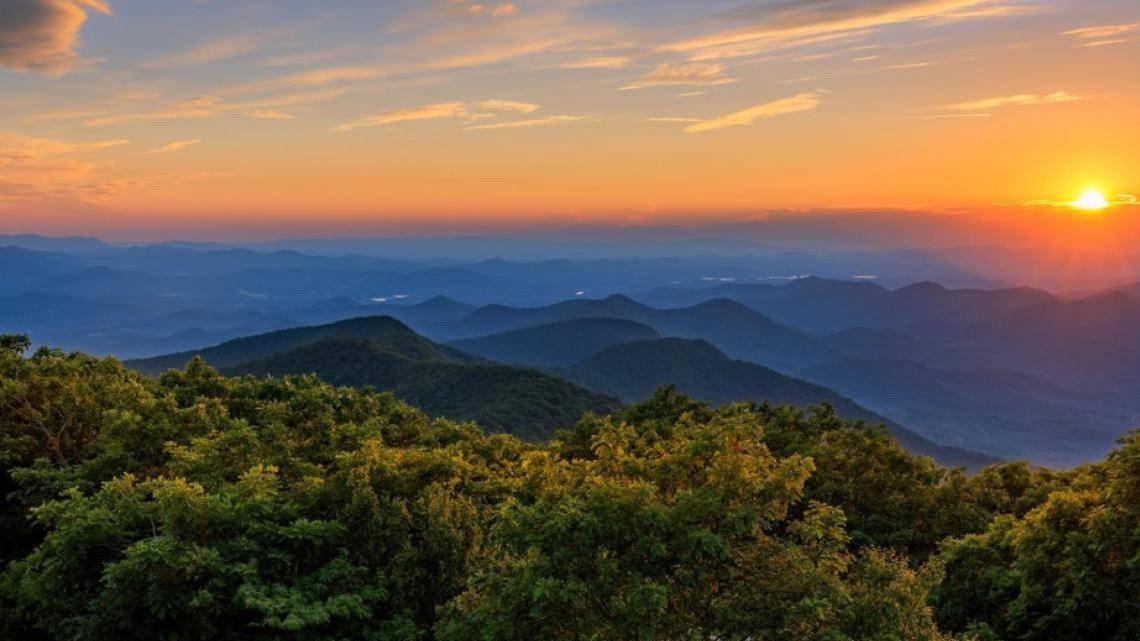
Mike Adams’ Balloon Loft
The birth of Adams Balloons originated in 1971 with Mike Adams' enormous amount of enthusiasm for the potential of the modern hot air balloon. In the beginning, with very few resources progress was slow but over a period of 10 months, serial number one took shape. Work at the drawing board and shopping for the perfect materials took most of the time.
What was a home to Mike Adams became a workshop where nights and weekends were spent designing and making the balloon. Week days were spent working to make money to support the ballooning hobby until 1973 when balloon building became a full time job. The fledgling company was primarily a flying business that built its own balloons and a few balloons here and there for other people.
The regular flight activity stimulated new designs and many refinements of existing designs while basic attitudes and philosophies about the standard balloon design became firmly established. The early balloons flew quite well but needed frequent repairs; the philosophy at Adams soon became “redesign rather than repair.”
Innovation
Ballooning was, and is supposed to be fun, and repairs have never been fun; the end result was Adams designing a versatile and rugged balloon that would spend more time in the air and not in the repair shop. From the onset, repairs seemed frustrating on any balloon so modifications began almost immediately.
Since the throat of the balloon was guaranteed to get the brunt of the radiant burner heat, Nomex was added to the bottom panel of the balloon. This fire-retardant fabric was the perfect choice to prevent burns at the mouth and soon the other manufacturers followed.
Next, stronger fabric was desired to extend the life of the balloon. From the wear and tear of ground handling, UV rays and Georgia's envelope-eating pine trees, fabric weight was increased for strength and longevity. Other high temperature fabrics were considered but ultimately Nylon was the final choice.
While other balloon companies focused on manufacturing bulbous balloons of either eight or twelve gores, Adams recognized that a smooth horizontal construction would allow for perfect artwork to be applied to the side of an envelope. As a result Adams adopted a flat sixteen gore design, whatever the envelope size.
Adams Balloons always offered a choice of deflation systems with its envelopes, including both parachute valves and the lightning-fast pop-top. Extremely popular with owners, the rapid deflation pop-top is perhaps the single most distinctive feature that the ballooning community associates with Adams’ envelopes.
It took substantially different basket designs to come up with the end result. The distinctive square/ round standard baskets are beautiful and simple yet strong. In 1975, the Smithsonian Air and Space Museum chose Adams for its modern gondola display and the basket is still on display representing a modern hot air balloon. Adams gondolas are the most rugged available on the market and the standard of excellence was set 40 years ago.
The Adams burner has an ingenious heat exchange manifold to keep the O-rings warm on cold winter days so they do not leak. Redundant blast valves and pilot lights have all been part of Adams evolutionary success.
The First Special Shape
Adams also built the very first Type Certified Special Shape.
Working with Kentucky Fried Chicken, Adams designed a KFC Chicken envelope with a matching Chicken Bucket basket.
In 1975, the complete balloon was tested and then submitted for approval with the FAA issuing a Standard Type Certificate in early 1976. Two Chickens were built and both balloons earned Standard Airworthiness Certificates.
More early work of Mike Adams can be found at the wonderful ballooninghistory.com.
Andy Richardson’s Adams Balloons
Andy Richardson purchased the Adams type certificates in 2014 and set up his company, Adams Balloons LLC, in Albuquerque, New Mexico, the world capital of hot air ballooning. The resumption of the historic and beloved line of aerostats made headlines throughout the ballooning community. Production peaked in 2017 with over 20 balloons produced that year. In addition to the classic Adams envelope models, many special shapes were built under the Adams name that still delight crowds all around the world. In 2019, Andy embarked on the process to move the production headquarters to his hometown of Bloomington, Indiana. The factory opened for production as a satellite facility in 2020, with both sites producing balloons for the next two years.